At Ven-Tech Subsea, we take pleasure in disseminating news about emerging technologies and images, especially Remote Inspection Services.
This includes showing our fleet of autonomous underwater vehicles (AUVs) and remotely operated vehicles (ROVs) for Remote Inspection Services, particularly when they are in use doing remote inspections in the real world.
In addition to being fun and interesting, ROVs are a crucial tool for deploying the technology we employ to collect data.
A condition evaluation is only as good as the information it includes when it comes to finishing an inspection of your underwater assets.
Both the technique for gathering data and the platform for deploying it are covered by remote inspection technology.
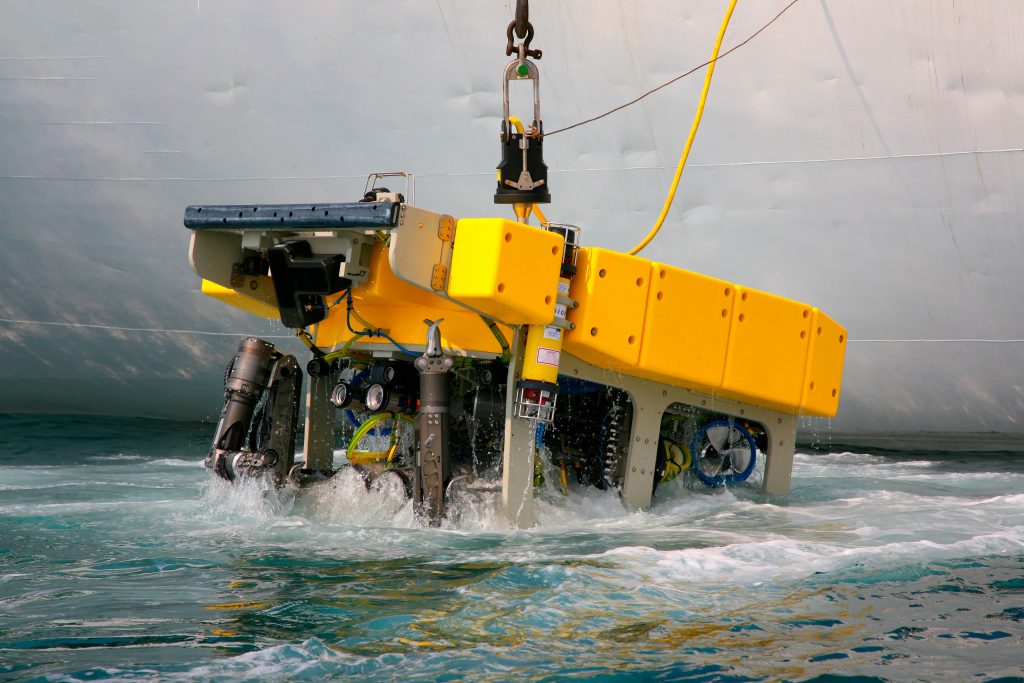
Remote Inspection Technology
Ven-Tech Subsea employs ROVs that may be customised and have different penetration distances, some of which are small enough to fit through a typical manhole access (about the size of carry-on luggage). Large ROVs can tether travel far distances, all the while transmitting data to the ROV operator and crew of technicians in real time. AUVs can be any size and travel any distance, but because they are untethered, their mobility is constrained by their battery life. The most recent tools and technologies can be installed on these systems
High-definition (HD) and standard-definition (SD) digital video
Both above and below the waterline, HD and SD cameras can record live video and video stills.
The video is viewed in real-time and captured onto a data recording computer when used during an examination.
In order to gather visual information and enable virtual walkthroughs in dry and tight space conditions, Ven-Tech Subsea additionally makes use of a 360-degree camera/video array.
One or Two Multi-beam Sonars
Two-dimensional (2D) and three-dimensional (3D) multi-beam imaging sonar provides valuable feature detection capabilities for the inspection of variances in surface texture.
Side-scan Sonar
A side-scan sonar (SSS system) can be mounted on any vessel, custom-designed frame, or ROV. The resulting processed sonar imagery results in a mosaic of the full face of the dam structure.
WireScan
For above and below water inspections, WireScan uses laser for high precision measurements that can be combined with 3D data, resulting in high point density georeferenced data capable of accuracy in sub-millimeters.
Ultrasonic (UT)
Various ultrasonic gauges from Ven-Tech Subsea are used to precisely assess metal thickness through corrosion and coating. Additionally, Ven-Tech Subsea has collaborated with a specialised concrete testing business to create an underwater ultrasonic concrete testing array that can reveal concrete’s mechanical properties.
Saw, hydraulic (Deep Trekker)
According to Ven-Tech Subsea’s specifications, Deep Trekker created and constructed a hydraulic saw. This saw has been used to get access to check and survey low-level outputs, intakes, and penstocks because it can be lowered by crane in up to 800 feet of water.
LiDAR
Above and below the water’s surface, a LiDAR (Light Detection and Ranging) scanner gathers three-dimensional (3D) point cloud data.
The available platforms will change as remote inspection technology develops and becomes more accessible.
For example, Ven-Tech Subsea has used airborne drones for inspections in out-of-water locations and is investigating the usage of walking robots and cutting-edge autonomous underwater vehicles.
For the deployment of sensors and the collecting of data from sensors, there are numerous new and in use technologies.
By customising the inspection platforms with the best-suited sensors, the appropriate technology may be deployed to get the information that is required.
Every evaluation must be able to give the client all the details they require to decide intelligently about the state of their asset.
If you want to learn more about how to determine the best technology to use for your inspection, contact us today.